Homepage » Metal Etching »
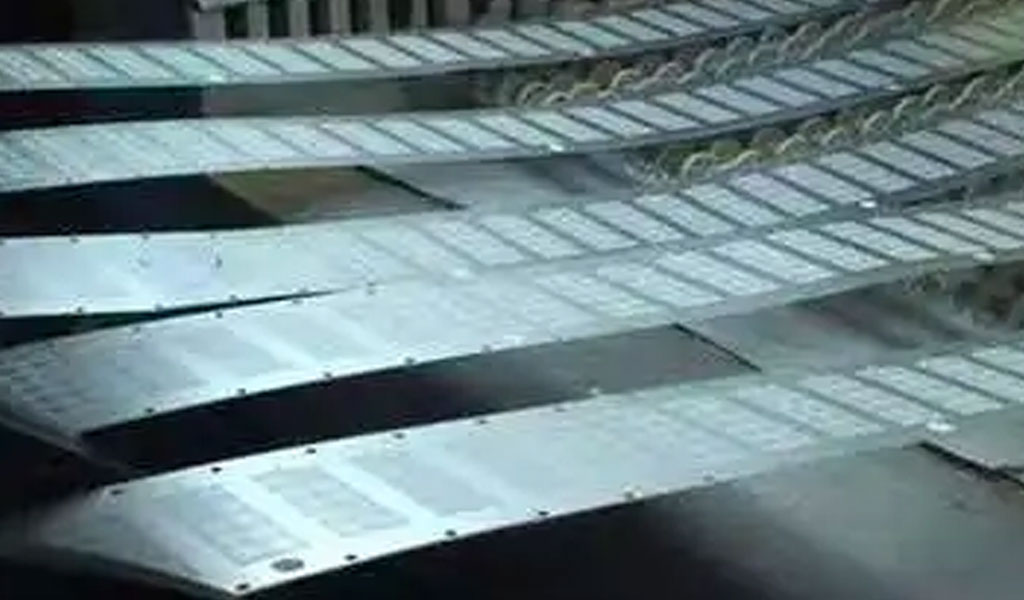
Roll-to-Roll Continuous Etching
Roll-to-roll continuous etching, also known as reel-to-reel processing, is a high-throughput manufacturing process used to fabricate flexible electronics, advanced materials, and microelectromechanical systems (MEMS). This technique involves the continuous processing of a flexible substrate, typically a metal foil or polymer film, which is unwound from a feed roll, passed through various etching stations, and then rewound onto a take-up roll.
The process enables the large-scale, cost-effective production of intricately patterned materials and devices, making it essential for industries such as electronics, photovoltaics, and flexible displays.
Historical Context of Roll-to-Roll Continuous Etching
Roll-to-roll continuous etching has its roots in the broader history of roll-to-roll (R2R) manufacturing, a technique that originated in the early 20th century. The development and adaptation of R2R processes have played a significant role in various industries, evolving significantly to meet the demands of modern technology. The historical context of roll-to-roll continuous etching can be understood through several key milestones:
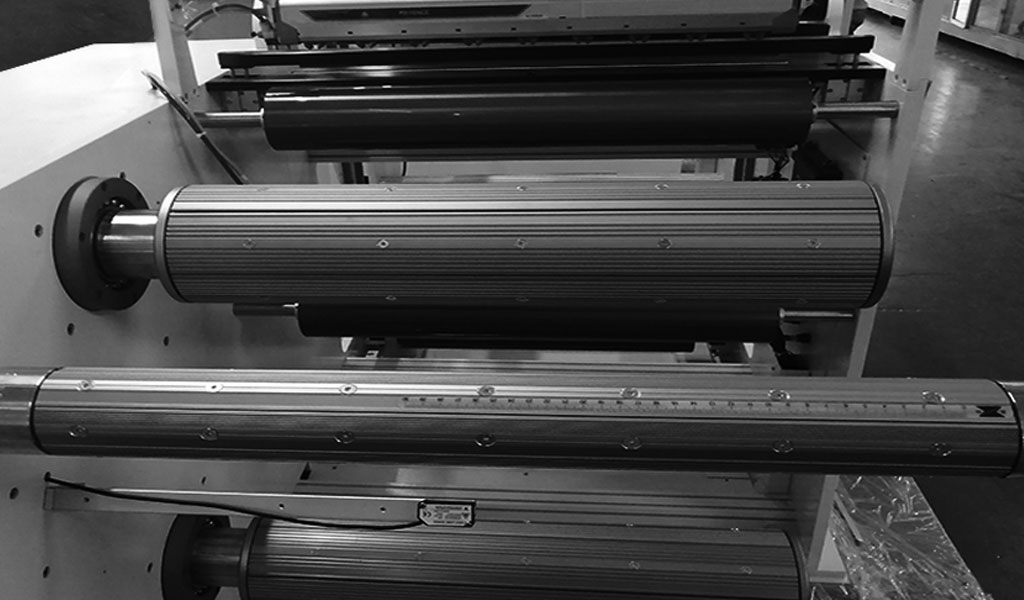
Early Beginnings
The concept of roll-to-roll processing began with the need to produce photographic films efficiently. In the 1920s and 1930s, companies like Eastman Kodak pioneered the continuous processing of photographic films, which involved coating, drying, and developing photographic emulsions on flexible substrates. This early application of R2R technology laid the groundwork for future innovations in continuous processing.
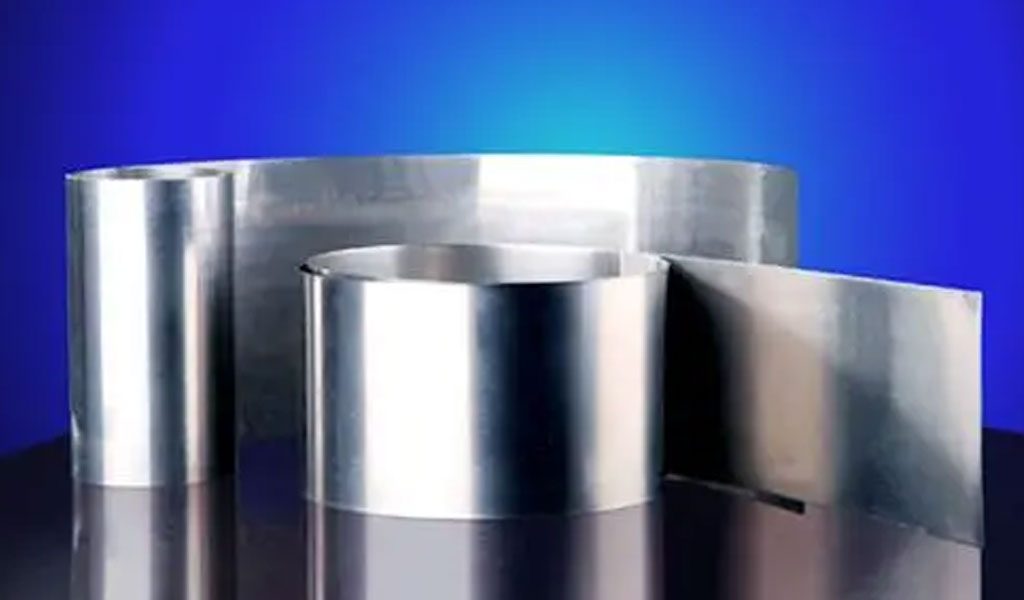
Mid-20th Century Developments
As the demand for miniaturized and flexible electronic components grew in the mid-20th century, the potential for roll-to-roll processing expanded beyond photographic films.
The development of printed circuit boards (PCBs) in the 1940s and 1950s highlighted the need for efficient methods to produce fine patterns on substrates. Although early PCB manufacturing relied heavily on batch processes, the principles of R2R processing began to influence thinking about continuous production methods.
Advent of Flexible Electronics
The 1960s and 1970s saw significant advances in materials science, particularly with the development of flexible polymers and thin metal foils. These materials were well-suited for roll-to-roll processing, leading to increased interest in continuous etching techniques. During this period, researchers and engineers explored the feasibility of applying R2R methods to etch intricate patterns on flexible substrates, particularly for applications in emerging fields such as flexible electronics and printed circuits.
Technological Innovations in the 1980s and 1990s
The 1980s and 1990s were marked by significant technological innovations that propelled roll-to-roll continuous etching into the mainstream. Key developments included:
- Advances in Photolithography: Improvements in photolithographic techniques allowed for the precise patterning of photoresists on flexible substrates. This enabled the creation of fine, high-resolution patterns necessary for modern electronics.
- Introduction of Dry Etching: The development of dry etching techniques, such as plasma etching and reactive ion etching (RIE), offered greater control over etch profiles and reduced the limitations of wet etching processes. This was particularly important for achieving anisotropic etching, which is critical for creating vertical sidewalls in microelectronic devices.
- Materials Engineering: The development of new polymer films, such as polyimide and polyethylene terephthalate (PET), provided substrates with excellent mechanical and thermal properties. These materials were ideal for roll-to-roll processing and could withstand the harsh conditions of etching processes.
Rise of Flexible and Printed Electronics
The late 1990s and early 2000s saw the rise of flexible and printed electronics, driven by the increasing demand for lightweight, portable, and flexible devices.
Roll-to-roll continuous etching played a crucial role in this transformation, enabling the mass production of flexible circuits, displays, and sensors. Companies and research institutions focused on refining R2R etching techniques to improve yield, resolution, and throughput.
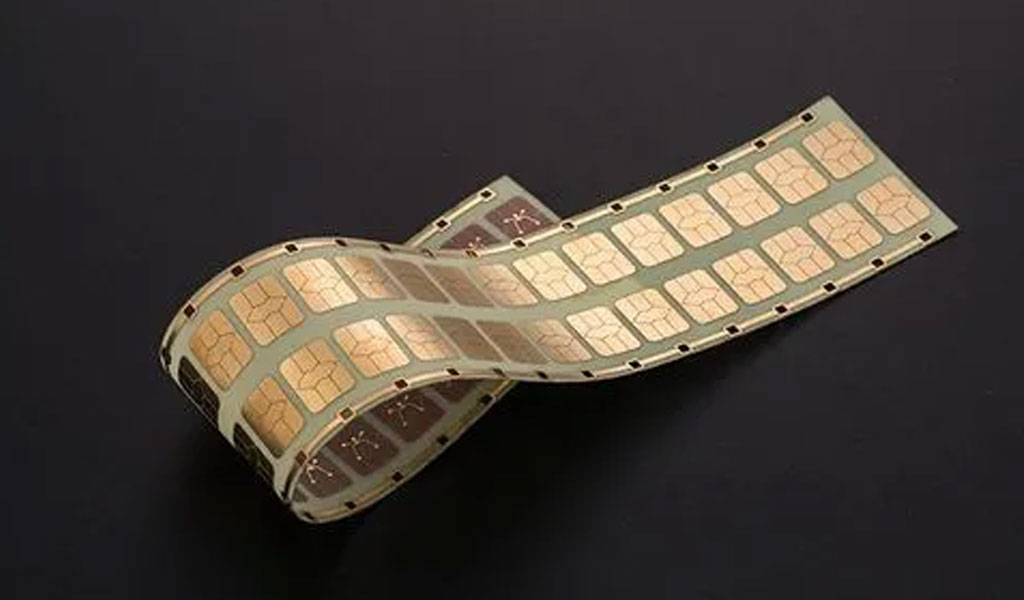
Recent Advances and Applications
In the 21st century, roll-to-roll continuous etching has become a cornerstone of advanced manufacturing, with applications spanning numerous industries. Key developments in recent years include:
- Flexible Displays: The development of flexible organic light-emitting diode (OLED) displays has been a major driver for roll-to-roll etching. Companies like LG and Samsung have leveraged R2R processing to produce bendable and foldable screens for smartphones, tablets, and wearable devices.
- Solar Cells: Roll-to-roll continuous etching is critical for the production of thin-film solar cells, which offer a lightweight and flexible alternative to traditional silicon-based solar panels. This has enabled the integration of solar cells into a variety of surfaces and structures, expanding their applications.
- Wearable Technology: The rise of wearable electronics, such as fitness trackers and medical sensors, has further highlighted the importance of roll-to-roll etching. These devices require flexible and durable circuits that can conform to the human body, making R2R etching an ideal manufacturing method.
- Microelectromechanical Systems (MEMS): Roll-to-roll continuous etching is increasingly used in the production of MEMS devices, which are essential components in a wide range of applications, from automotive sensors to medical devices.
Future Directions
As technology continues to advance, the future of roll-to-roll continuous etching looks promising. Ongoing research and development efforts aim to address current challenges and expand the capabilities of R2R processing. Key areas of focus include:
- Nanofabrication: Developing techniques for roll-to-roll etching at the nanoscale, enabling the production of even smaller and more complex devices.
- Hybrid Processes: Integrating roll-to-roll etching with other manufacturing techniques, such as additive manufacturing and laser processing, to create multifunctional devices with enhanced performance.
- Sustainable Manufacturing: Reducing the environmental impact of roll-to-roll etching through the development of eco-friendly etchants, recycling methods, and energy-efficient processes.
The historical context of roll-to-roll continuous etching reflects a century-long evolution of technology and innovation. From its early beginnings in the photographic film industry to its current role in advanced manufacturing, R2R etching has continuously adapted to meet the demands of modern technology, enabling the mass production of flexible, lightweight, and high-performance electronic devices.
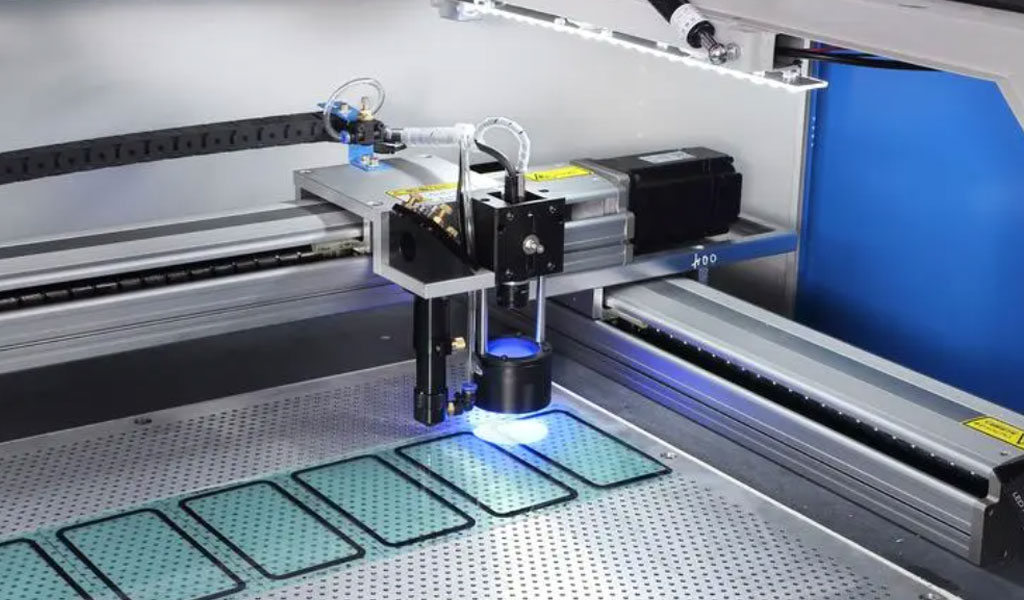
Materials and Substrates in Roll-to-Roll Continuous Etching
Roll-to-roll continuous etching, a cornerstone in the fabrication of flexible electronics and advanced materials, relies on a variety of substrates and etching materials. The choice of these materials is crucial for achieving the desired properties in the final products and ensuring compatibility with the etching processes. This section delves into the types of materials used, their properties, and their applications in roll-to-roll continuous etching.
Metal Roll-to-Roll Continuous Etching
- Copper: Widely used due to its excellent electrical conductivity, copper is a preferred substrate for creating flexible circuits and interconnects. Its relatively low cost and good adhesion properties make it suitable for high-volume production.
- Aluminum: Known for its lightweight and corrosion-resistant properties, aluminum is used in applications where weight reduction is critical, such as in aerospace and portable electronics.
- Stainless Steel: Offers excellent mechanical strength and resistance to corrosion. It is often used in harsh environments where durability is paramount, such as in medical devices and industrial sensors.
Polymer Roll-to-Roll Continuous Etching
- Polyimide (PI): Known for its high thermal stability, chemical resistance, and mechanical properties, polyimide is a common substrate in flexible electronics, especially for applications requiring high-temperature processing.
- Polyethylene Terephthalate (PET): PET is valued for its flexibility, transparency, and chemical resistance. It is widely used in the production of flexible displays and solar cells.
- Polyethylene Naphthalate (PEN): PEN offers better thermal stability and mechanical properties compared to PET, making it suitable for applications requiring higher performance, such as high-frequency circuits.
Composite Materials Roll-to-Roll Continuous Etching
- Glass-Fiber Reinforced Polymers: These composites combine the flexibility of polymers with the strength of glass fibers, resulting in substrates that are both durable and lightweight. They are used in applications requiring robust mechanical properties.
- Metal-Polymer Laminates: These materials combine the conductive properties of metals with the flexibility of polymers, offering an ideal balance for creating flexible electronic devices.
How Does Roll-to-Roll Continuous Etching Work?
Roll-to-roll (R2R) continuous etching is a sophisticated manufacturing process designed to produce flexible electronics and advanced materials efficiently and at scale. The process involves a continuous strip of material, typically a metal or polymer film, being fed through a series of stations that perform various steps of the etching process. This method leverages the principles of continuous production to achieve high throughput, precision, and cost-effectiveness.
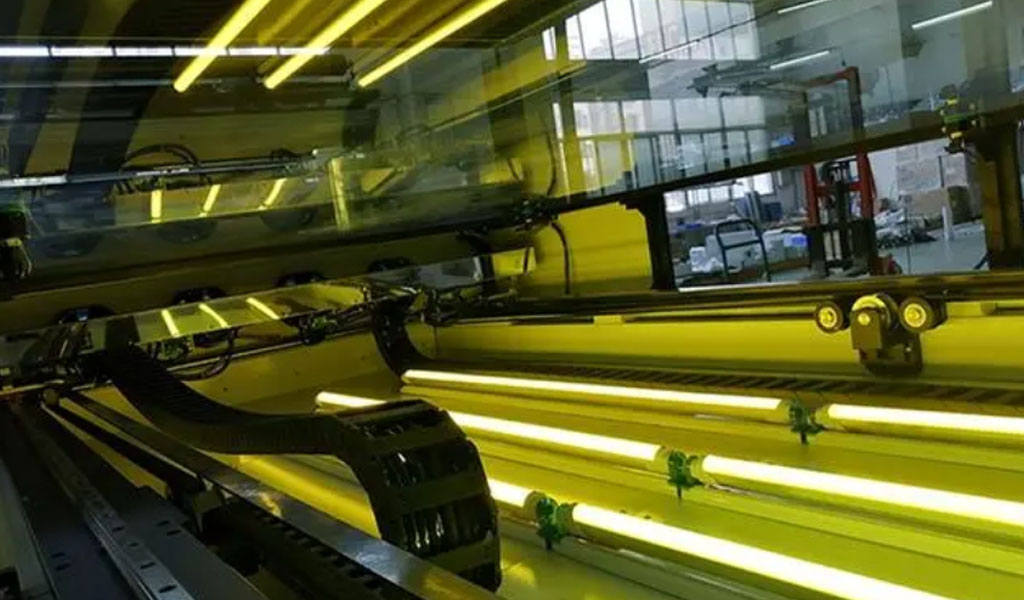
Here, we provide a detailed overview of how roll-to-roll continuous etching works, breaking down the process into its essential stages and components.
Key Components of Roll-to-Roll Continuous Etching Systems
Unwinder: This component holds the roll of the substrate material and feeds it into the etching line. It ensures consistent tension and alignment as the substrate is unwound and fed into the system.
Cleaning Station: The substrate undergoes a cleaning process to remove any contaminants or residues that could affect the etching quality. Common cleaning methods include solvent cleaning, ultrasonic cleaning, and plasma cleaning.
Coating Station: Here, a photoresist or other masking material is applied to the substrate. The coating can be applied using various techniques, such as spin coating, slot-die coating, or inkjet printing, depending on the substrate material and desired pattern resolution.
Drying/Oven Station: After coating, the substrate typically passes through a drying or curing station to solidify the photoresist layer. This step is crucial for ensuring that the photoresist adheres properly to the substrate and achieves the desired thickness and uniformity.
Exposure Station: The coated substrate is exposed to a pattern using photolithography or direct-write laser systems. Photolithography involves exposing the photoresist through a mask, which defines the pattern to be etched. Direct-write systems use a focused laser beam to write the pattern directly onto the photoresist.
Development Station: After exposure, the substrate moves to the development station, where the exposed photoresist is developed, leaving behind the patterned photoresist on the substrate. This step reveals the areas of the substrate that will be etched.
Etching Station: The substrate then enters the etching station, where the exposed areas are etched away. Depending on the material and desired etch profile, wet etching, dry etching, electrochemical etching, or laser etching techniques may be used. Each method has its specific equipment and parameters:
- Wet Etching: Involves immersing the substrate in a chemical bath that selectively removes material. The etchant and process parameters (e.g., temperature, concentration) are carefully controlled.
- Dry Etching: Utilizes plasma or reactive gases to etch the material. Equipment such as plasma reactors or reactive ion etching (RIE) systems are used to achieve precise etch profiles.
- Electrochemical Etching: Involves an electrolytic cell where the substrate serves as an electrode, and material is removed through controlled electrochemical reactions.
- Laser Etching: Employs focused laser beams to ablate material. Laser systems are configured to achieve high precision and minimal thermal damage.
Post-Etch Cleaning: After etching, the substrate undergoes a cleaning process to remove any etchant residues and undeveloped photoresist. This step ensures that the substrate is free of contaminants that could affect subsequent processing or the performance of the final product.
Inspection and Quality Control: The etched substrate is inspected for defects, dimensional accuracy, and pattern fidelity. Quality control methods may include optical microscopy, scanning electron microscopy (SEM), and surface profilometry. Automated inspection systems can provide real-time feedback and adjustments to the process.
Rewinder: The final step in the process involves rewinding the etched substrate onto a take-up roll. The rewinder ensures consistent tension and alignment, preparing the substrate for further processing or integration into final products.
Detailed Process Flow
Substrate Preparation: The substrate, such as a metal foil or polymer film, is loaded onto the unwinder. Ensuring the substrate is clean and free of defects is critical for achieving high-quality etching results.
Coating: The substrate is fed through the coating station, where a photoresist layer is uniformly applied. The choice of coating method depends on the substrate material, the viscosity of the photoresist, and the desired thickness.
Drying/Curing: The coated substrate passes through a drying oven or UV curing station to solidify the photoresist layer. This step ensures that the photoresist is fully adhered and ready for patterning.
Exposure: In the exposure station, the photoresist-coated substrate is exposed to a pattern using photolithography or laser writing. Photolithography involves aligning a photomask with the substrate and exposing it to UV light, which transfers the pattern onto the photoresist. Laser writing uses a focused laser beam to directly inscribe the pattern onto the photoresist.
Development: The substrate then moves to the development station, where the exposed photoresist is developed. The development process selectively removes the exposed areas of the photoresist, revealing the underlying substrate material.
Etching: The developed substrate enters the etching station. Depending on the etching technique:
- Wet Etching: The substrate is immersed in a chemical bath that etches away the exposed material. The etchant, temperature, and immersion time are carefully controlled to achieve the desired etch depth and profile.
- Dry Etching: The substrate is placed in a plasma reactor or RIE system, where reactive gases etch the exposed material. Parameters such as gas flow rate, pressure, and power are optimized for precise etching.
- Electrochemical Etching: The substrate serves as an electrode in an electrolytic cell, where controlled electrochemical reactions remove the exposed material. Voltage, current, and electrolyte composition are adjusted to achieve the desired etch.
- Laser Etching: A focused laser beam scans the substrate, ablating the exposed material. Laser power, scan speed, and focal length are adjusted for precise material removal.
Post-Etch Cleaning: After etching, the substrate undergoes a cleaning process to remove any remaining etchant residues and undeveloped photoresist. This ensures the substrate is free of contaminants and ready for further processing.
Inspection and Quality Control: The etched substrate is inspected using various techniques to ensure pattern fidelity and dimensional accuracy. Automated inspection systems provide real-time feedback and allow for process adjustments to maintain consistent quality.
Rewinding: The final step involves rewinding the processed substrate onto a take-up roll. The rewinder ensures consistent tension and alignment, preparing the substrate for subsequent processing or integration into final products.
Advantages and Applications
The roll-to-roll continuous etching process offers several advantages:
- High Throughput: The continuous nature of the process allows for the rapid production of large volumes of material.
- Cost-Effectiveness: The ability to process substrates in a continuous manner reduces production costs, making it ideal for high-volume manufacturing.
- Precision: Advanced etching techniques, such as dry etching and laser etching, provide high-resolution patterning capabilities.
- Flexibility: The process is adaptable to a wide range of materials and applications, from flexible electronics to MEMS devices.
Applications
- Flexible Electronics: Roll-to-roll etching is used to produce flexible circuits, sensors, and displays. The ability to etch fine patterns on flexible substrates is essential for developing lightweight and bendable electronic devices.
- Photovoltaics: The process is employed in the manufacturing of thin-film solar cells, where precise patterning of the active layers enhances light absorption and electrical performance.
- MEMS: Roll-to-roll etching is used to fabricate microscale devices such as accelerometers, gyroscopes, and pressure sensors. The process enables high-volume production with consistent quality.
- RFID Tags: The technique is utilized in creating antenna patterns for RFID tags, used in logistics, inventory management, and contactless payment systems.
- Biomedical Devices: Roll-to-roll etching is applied in the production of flexible bioelectronic devices, such as wearable sensors and implantable medical devices. The ability to etch biocompatible materials with high precision is critical for these applications.
Roll-to-roll continuous etching is a vital manufacturing process that enables the large-scale production of flexible and miniaturized electronic components. By integrating various etching techniques and optimizing process parameters, R2R etching achieves high throughput, precision, and cost-effectiveness. This process is indispensable for industries ranging from electronics to biomedical devices, offering a versatile and efficient solution for modern manufacturing challenges.
Advanced Precision Roll-to-Roll Etching Services and Parts Manufacturer
Looking for low cost Roll-to-Roll Etching parts with unparalleled quality? BE-CU Etching Co., Limited is a professional China Etching company provides superior precision Roll-to-Roll Etching services with advanced machines including chemical etching line and acid etching line from the general photo etching and accomplished machinists. Our experienced operators proficient in CAD (computer-aided design) and CAM (computer-aided manufacturing) programs are always finding the best way to produce the highest quality Roll-to-Roll Etching parts & components for clients.
With strong capabilities and extensive experiences, we can works with aluminum, beryllium copper, brass, bronze, carbon steel, copper, Invar®, Kovar®, Monel®, Nichrome®, nickel, nickel silver, phosphorous bronze, spring steel, stainless steel and steel. Shearing, cutting, chemical milling, blanking and photochemical milling processes also provided. Serves the aerospace, architecture, transportation, automation, automotive, construction, electronics, electrical, government, marine, military, medical and waste management industries. Send your inquiry or drawing fast to get an online etching quote.
-
Copperplate Engravings Of World Famous Works
-
Artistic Etched Copper Shielding Electronics Playing Cards with Patterns
-
Precision Etched Titanium Alloy Odor Eliminator Perforated Plates
-
High-End Etched TC4 Titanium Alloy Filters
-
Aluminum Alloy 7075 Etched Microphone Grille
-
Molybdenum Screen and Spacecraft Electron Tube Grid Etching
-
Metal Etching Car Audio Modified Insulation Chips Shock Absorber Board Acoustic
-
Etching 6.0 Inch Molybdenum Alloy Subwoofer Speaker Grill Guard Protector Cover for Home Audio
-
Precision Etching Titanium Alloy Hanging Fixture for Anodizing
-
Stainless Steel 316L Etching Tea Strainer
-
Zinc Alloy Nameplate Etching For Bags Logo/Signs
-
Russian Mythology Character Metal Nameplate Badge Etching
Metal Etching Certification,Equipment List and Quality
We are committed to enlisting the full support of all employees to continuously improve our processes and enhance quality, thereby fulfilling our customer's needs with defect free products and services, on time and every time
- ISO 9001:2015 certified
- Compliance in DFARS materials sourcing requirements
- Strict compliance with PPAP and Process FMEA
- Fully compliant with the exacting requirements of our customers
- ITAR registered
- NIST cybersecurity standard compliant
- Proprietary Patented quality systems
- Skilled in KanBan and other customer driven quality and inventory management systems
Metal Etching Material
BE-CU is experienced in precision etching various metals, allowing customers the freedom to specify components in hundreds of different materials.
The Surface Treatment Of Metal Etching Parts
Do you want your etching parts to be more corrosion-resistant or get a specific look? Metal finishing service is a essential choice to achieve your design perfectly. BE-CU – metal-etch.com is an accomplished finished parts manufacturer, our workers and craftsman are capable to provide precision metal etching services and a wide range of finishing services including aluminum anodizing, painting, passivation, electroplating, powder coating, polishing, black oxide, conversion coating, abrasive blasting, etc. We offers several common surface finishes to help improve functionality and aesthetics.
- Anodizing (Anodized)
- Passivation
- Plating (Electroplating)
- Painting
- Black Oxide (Hot Blackening)
- Polishing
- Powder Coating
- Heat Treatment
- Satin Finish
- Abrasive blasting (Sandblasting)
- Conversion coating
- Tungsten carbide coating
After browsing a list of metal finishing services, select a process based on essential considerations, like production time, cost-effectiveness, part tolerance, durability and applications. High-tolerance metal etching parts are not recommended to apply secondary metal surface finish, because the treatment may change the sizes of the finished part through removing or adding a small amount of materials.
Other requirements or custom designs, welcome to contact us for a free quote fast!