Homepage » Metal Etching »
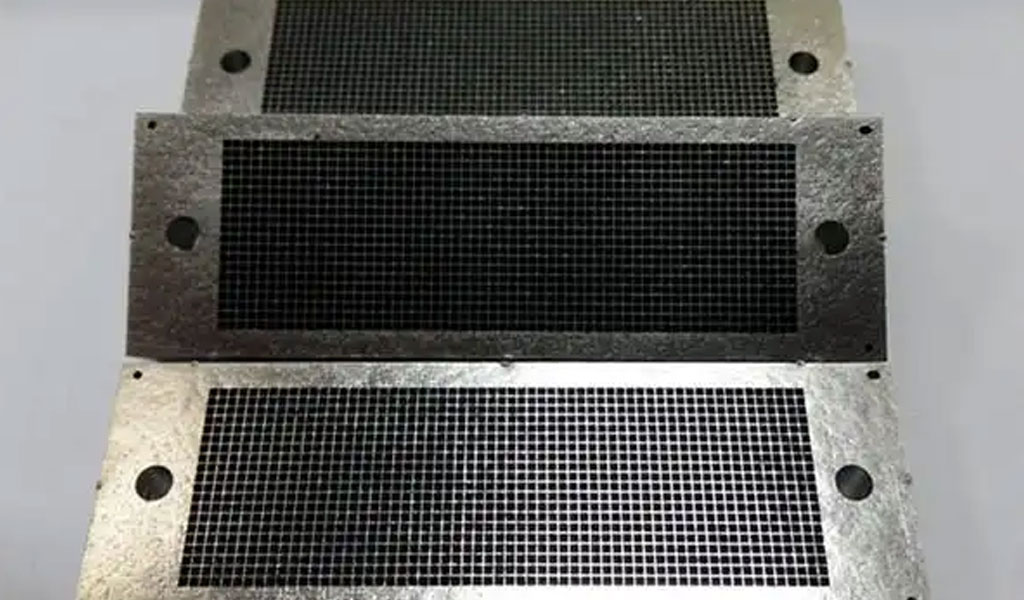
Vacuum Diffusion Bonding
Vacuum Diffusion Bonding is a solid-state joining process where two or more materials are bonded together at elevated temperatures in a vacuum environment. The process involves the diffusion of atoms between the surfaces of the materials to form a metallurgical bond without the use of fillers or adhesives. It is distinct from other bonding methods like welding, soldering, or brazing in that it does not involve the melting of the materials being joined. Instead, the materials remain in their solid state during the bonding process.
This technique is particularly valuable in industries requiring high-performance materials, such as aerospace, automotive, and electronics. It provides the ability to join dissimilar materials, create strong, durable bonds, and achieve precise control over the bond’s properties.
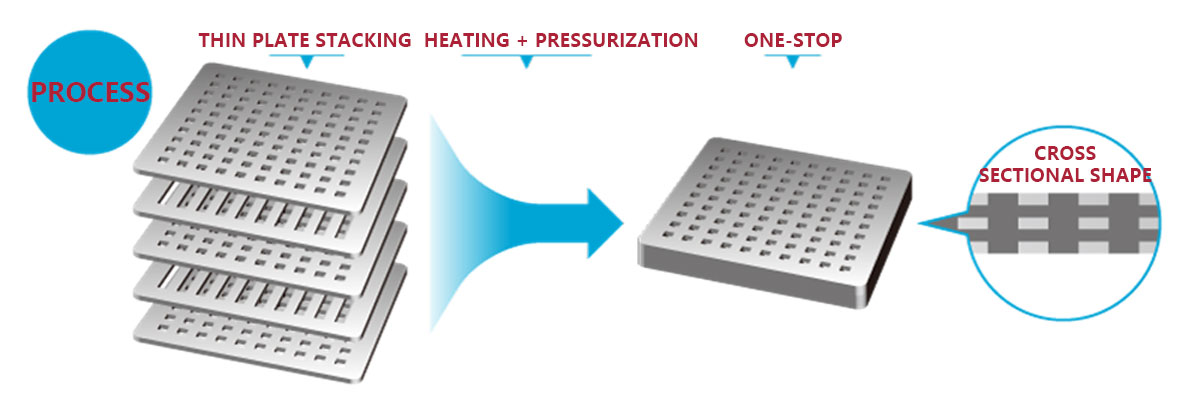
The concept of diffusion bonding dates back to the mid-20th century, driven by the need for stronger, more reliable materials in advanced manufacturing. It was originally developed for use in the aerospace industry, where the combination of high-performance materials was essential for applications such as engine components and structural elements. Vacuum Diffusion Bonding (VDB) emerged as a refinement of traditional diffusion bonding, addressing limitations related to oxidation and contamination of the materials being joined. By using a vacuum environment, VDB significantly reduces the risk of surface oxidation, ensuring the quality and strength of the bond.
Over the years, as the demand for high-performance materials grew in various industries, VDB found applications in a variety of fields, including semiconductor manufacturing, medical devices, and even nuclear reactors, where reliability and precision are paramount.
Vacuum Diffusion Bonding Services for Metal Parts
Vacuum diffusion welding offers high-quality joints, requires no post-welding processing, and can be automated. It does not cause plastic deformation and can weld different types of materials, even those with significant differences. This includes dissimilar metals and materials that are completely immiscible in terms of metallurgy, such as metal and ceramics.
The mechanical strength, thermal stability, sealing properties, corrosion resistance, and elasticity of the welded joints produced by vacuum diffusion welding meet the technical requirements for critical components. Notably, the size of the workpieces welded by diffusion welding can range from a few microns to several meters. Industries such as mechanical manufacturing, tractors, tools, electronics, aerospace, instrumentation, shipbuilding, food machinery, and others have applied vacuum diffusion welding to manufacture electrical vacuum devices, tools, brakes, hydraulic machinery components, bimetallic parts, composite-bottom household cookware (which requires no surface treatment after welding), and more.
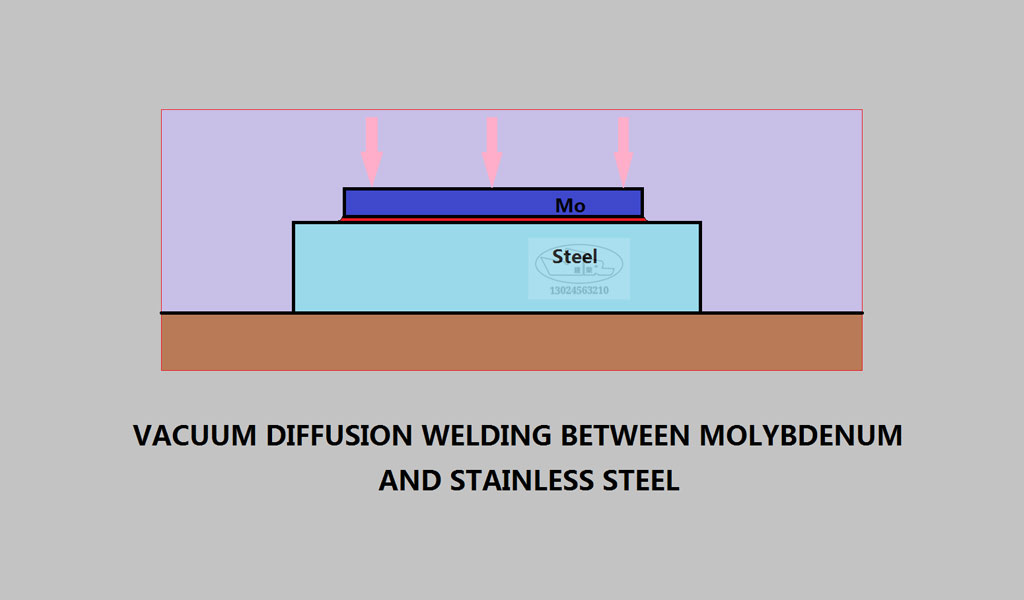
As of 2024, our company has been involved in the field of precision metal etching for 30 years and has consistently focused on the innovation, technological research and development, production, processing, and sales of precision metal etching and vacuum diffusion welding. We have explored a series of technical parameters and processing techniques for vacuum diffusion welding products. Our company has passed ISO9001 Quality Management System certification, ISO14001 Environmental Management System certification, TS 16949 certification for the automotive industry, and High-Tech Enterprise certification, among others. BE-CU has always prioritized technological development, establishing a professional laboratory and hiring and training high-tech talents. Our diffusion welding services can weld materials that are difficult to join using other methods, whether they are materials with poor plasticity or high melting points, or dissimilar metals that do not dissolve in each other or form intermetallic compounds during fusion welding, resulting in strong and durable welds. Therefore, vacuum diffusion welding is widely used in specialized fields.
Vacuum Diffusion Bonding For Metal Etching Parts
With our Vacuum Diffusion Bonding service, we can cater to both one-off prototypes and high-volume production requirements, enabling us to serve a diverse range of specialist component applications.
-
Copperplate Engravings Of World Famous Works
-
Artistic Etched Copper Shielding Electronics Playing Cards with Patterns
-
Precision Etched Titanium Alloy Odor Eliminator Perforated Plates
-
High-End Etched TC4 Titanium Alloy Filters
-
Aluminum Alloy 7075 Etched Microphone Grille
-
Molybdenum Screen and Spacecraft Electron Tube Grid Etching
-
Metal Etching Car Audio Modified Insulation Chips Shock Absorber Board Acoustic
-
Etching 6.0 Inch Molybdenum Alloy Subwoofer Speaker Grill Guard Protector Cover for Home Audio
-
Precision Etching Titanium Alloy Hanging Fixture for Anodizing
-
Stainless Steel 316L Etching Tea Strainer
-
Zinc Alloy Nameplate Etching For Bags Logo/Signs
-
Russian Mythology Character Metal Nameplate Badge Etching
Advantages of Vacuum Diffusion Welding
Vacuum Diffusion Bonding offers several significant advantages over other bonding methods:
- The vacuum diffusion welding process is conducted without the formation of a liquid phase, or only with a small transitional phase, and the joint is subsequently subjected to diffusion treatment. This ensures that the composition and structure of the joint are identical to the base material, with no residual cast structure, and the original interface disappears entirely. As a result, the physical, chemical, and mechanical properties of the base metal remain unchanged, and the material’s properties are not altered.
- Vacuum diffusion welding is suitable for welding both metal and non-metal materials, particularly when welding with conventional methods is difficult to achieve or when welding could severely damage the material’s performance and structure. This includes materials like dispersion-strengthened high-temperature alloys and fiber-reinforced boron-aluminum composites.
- Vacuum diffusion welding ensures even heating, with no deformation or residual stress in the workpiece. After welding, the workpiece maintains high geometric accuracy and shape, and it can undergo further mechanical processing, such as wire cutting, laser cutting, bending, stamping, and other operations.
- Vacuum diffusion welding can join materials that differ greatly in type, including dissimilar metals and materials like metal and ceramics, which are completely immiscible in terms of metallurgy.
Applications of Vacuum Diffusion Bonding
Vacuum Diffusion Bonding is used in a variety of industries, including:
- Aerospace: In the aerospace industry, VDB is used to join high-performance materials like titanium, aluminum, and nickel alloys to create components such as turbine blades, engine parts, and airframe structures.
- Automotive: VDB is used in the automotive industry for applications requiring lightweight, high-strength materials, such as engine components, transmission parts, and structural elements.
- Electronics: In the electronics industry, VDB is used to bond materials for heat sinks, connectors, and semiconductor packages, where precise control over thermal conductivity and electrical properties is essential.
- Medical Devices: The medical industry benefits from VDB in the production of components like surgical tools, implants, and diagnostic equipment, where material integrity and biocompatibility are critical.
- Nuclear Engineering: In nuclear engineering, VDB is used to bond materials for reactor components, where high temperature and radiation resistance are necessary.
- Semiconductor Manufacturing: VDB is used in the production of semiconductor components and devices, where high precision and contamination-free bonding are crucial.
Online Cooperate With Vacuum Diffusion Bonding Company
We are not resellers of other companies’ parts.That’s because we enjoy making a living by producing, not by earning commissions on other people’s work. We are a true Vacuum Diffusion Bonding service.
Your confidential files won’t be shared with third parties.
Be-cu works with customers all over the world to bring customers ideas to life with the highest quality Vacuum Diffusion Bonding on the planet. If you are looking for a partnership to help you apply new tools and technologies, or help you fully realize your design vision, let us help you move your business forward, contact our team ([email protected])or quote online today to get the conversation started.
Metal Etching Certification,Equipment List and Quality
We are committed to enlisting the full support of all employees to continuously improve our processes and enhance quality, thereby fulfilling our customer's needs with defect free products and services, on time and every time
- ISO 9001:2015 certified
- Compliance in DFARS materials sourcing requirements
- Strict compliance with PPAP and Process FMEA
- Fully compliant with the exacting requirements of our customers
- ITAR registered
- NIST cybersecurity standard compliant
- Proprietary Patented quality systems
- Skilled in KanBan and other customer driven quality and inventory management systems
Metal Etching Material
BE-CU is experienced in precision etching various metals, allowing customers the freedom to specify components in hundreds of different materials.
The Surface Treatment Of Metal Etching Parts
Do you want your etching parts to be more corrosion-resistant or get a specific look? Metal finishing service is a essential choice to achieve your design perfectly. BE-CU – metal-etch.com is an accomplished finished parts manufacturer, our workers and craftsman are capable to provide precision metal etching services and a wide range of finishing services including aluminum anodizing, painting, passivation, electroplating, powder coating, polishing, black oxide, conversion coating, abrasive blasting, etc. We offers several common surface finishes to help improve functionality and aesthetics.
- Anodizing (Anodized)
- Passivation
- Plating (Electroplating)
- Painting
- Black Oxide (Hot Blackening)
- Polishing
- Powder Coating
- Heat Treatment
- Satin Finish
- Abrasive blasting (Sandblasting)
- Conversion coating
- Tungsten carbide coating
After browsing a list of metal finishing services, select a process based on essential considerations, like production time, cost-effectiveness, part tolerance, durability and applications. High-tolerance metal etching parts are not recommended to apply secondary metal surface finish, because the treatment may change the sizes of the finished part through removing or adding a small amount of materials.
Other requirements or custom designs, welcome to contact us for a free quote fast!