Homepage » Metal Etching »
Electronic Etching – Metal Etching for Electronic Industries
Electronic etching is a sophisticated manufacturing process used primarily in the production of electronic components, particularly in the semiconductor and microfabrication industries. It involves the selective removal of material from a substrate, allowing for the precise definition of intricate patterns and features that are essential for the functionality of electronic devices. The development of electronic etching has revolutionized the production of integrated circuits, enabling the miniaturization and enhancement of electronic devices that have become ubiquitous in modern society.
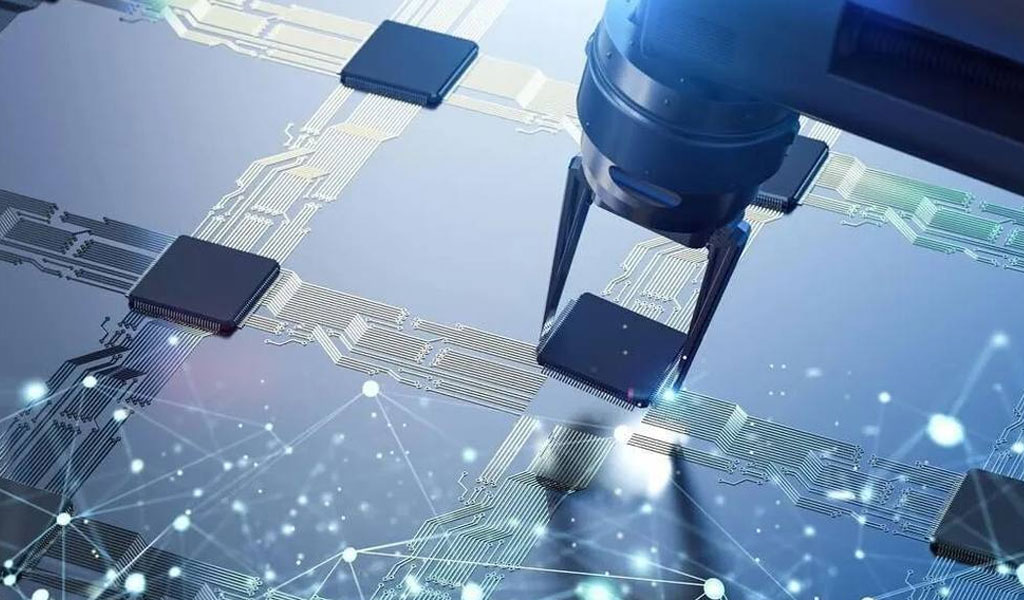
The origins of electronic etching can be traced back to the mid-20th century, coinciding with the advent of semiconductor technology. As the demand for smaller and more powerful electronic devices grew, the need for advanced etching techniques became paramount.
Traditional etching methods, which relied on mechanical processes, were insufficient for achieving the high levels of precision required for modern electronics.
Consequently, electronic etching methods were developed to meet these needs, utilizing chemical and physical processes to achieve finer resolutions and more complex geometries.
In the contemporary landscape of manufacturing, electronic etching plays a critical role in various applications, including the fabrication of microelectronic circuits, printed circuit boards (PCBs), and microelectromechanical systems (MEMS). The ability to create intricate patterns on a micro-scale is essential for the functionality of these devices, which are foundational to technology ranging from consumer electronics to advanced medical instruments.
Our Precision Electronic Etching Service
If you need electronic parts etched we are one of the most capable and affordable sources specializing in manufacturing custom etched parts on advanced photo etching machines with cnc precision. Through our Photo Chemical Etching process, the smallest and most complex designs are made possible such as electrical spring contacts, contact membranes, busbars, antennae and micro antennae, spring fingered contacts, heating elements and battery terminal as well as many other bespoke components to your own designs.
We can machine to print and accept the most common file formats including: .dwg .dxf .iges .step .sat as well as .pdf files. If you don’t see your file format here let us know. Please send us files to: [email protected] We can accept both small and large run jobs of custom electronic etching parts.
Our Etching Capabilities
- Etching of many grades of metal and more
- Combining Stamping, Laser Cutting,CNC machining and photochemical etching on sheets up to 2mm thick
- Etching of up to 0.025″ thick sheets as large as 22×12 inches
- Tolerances of ±.0005″ in many applications
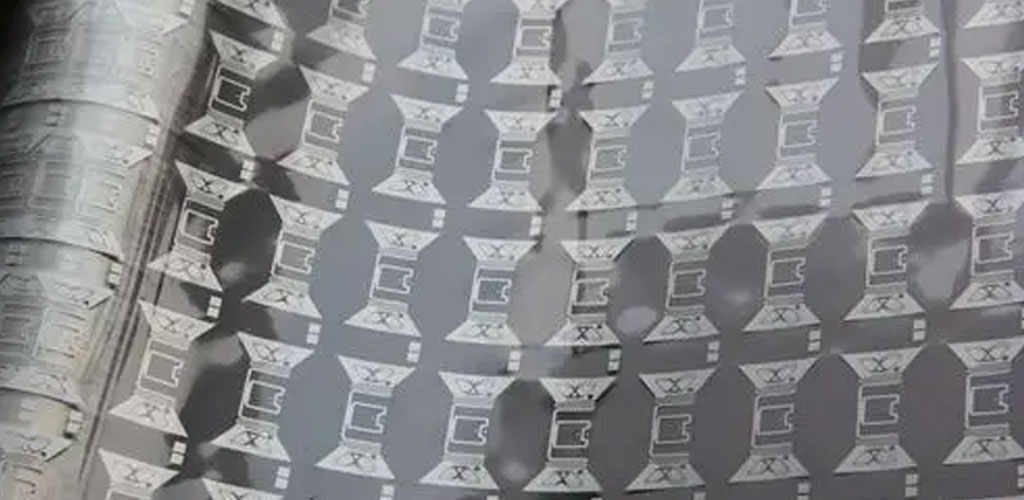
How To Etch Electronic Parts
Automated-Coating Automatic-Baking-Line Automatic-Shearing Coating-For-Etching-Parts Deinking Etching Exposure Inspection-For-Etching
Flexible Used Of Electronic Etching Technology
In the rapidly advancing realm of technology, the microelectronics industry is witnessing unprecedented innovations and breakthroughs. Among these advancements, etching technology has emerged as a pivotal force driving the evolution of the microelectronics sector. This article aims to explore the applications and advantages of etching within the electronics industry, analyzing its critical role in the microelectronics field.
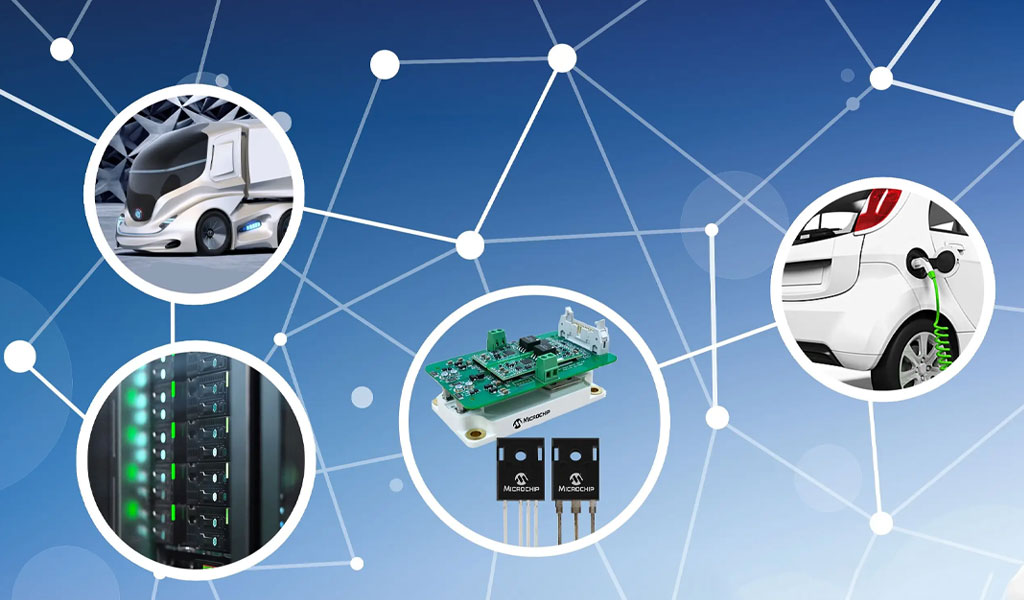
Firstly, etching technology plays a vital role in the manufacturing of integrated circuits (ICs). As the foundation of modern electronic devices, the IC fabrication process necessitates high precision and quality to ensure stable performance. Due to its high accuracy and controllability, etching is extensively employed in the fabrication of interconnect structures, capacitors, inductors, and other components within integrated circuits. By precisely controlling parameters such as etchant concentration, duration, and temperature, etching technology can create intricate circuit patterns and structures at micro-scale dimensions, thereby significantly enhancing the performance and reliability of integrated circuits.
Secondly, etching technology is also crucial in the manufacturing of Micro-Electro-Mechanical Systems (MEMS). As a miniaturized electromechanical system, MEMS have widespread applications in sensors, actuators, and beyond. Etching is employed to fabricate microstructures within MEMS, including miniature sensors and micro-motors. These microstructures exhibit advantages such as small size, lightweight, and low power consumption, broadening the potential applications of MEMS.
Moreover, etching technology plays an essential role in the fields of photonics and optoelectronics. As optoelectronic technology continues to advance, the manufacturing of photonic devices such as waveguides, lasers, and detectors increasingly demands precision and quality. With its high accuracy and flexibility, etching can produce photonic devices that meet these stringent requirements, thereby propelling the development of optoelectronics.
In the realm of biochip manufacturing, etching technology also holds considerable promise. Biochips serve as miniaturized platforms for biological analysis, with immense potential in gene sequencing and drug screening.
Etching can be utilized to fabricate microarray chips for high-throughput detection and analysis of biomolecules.
By precisely controlling the etching process, biochips can be produced with specific patterns and structures, providing robust support for biomedical research.In addition to these applications, etching technology offers numerous advantages.
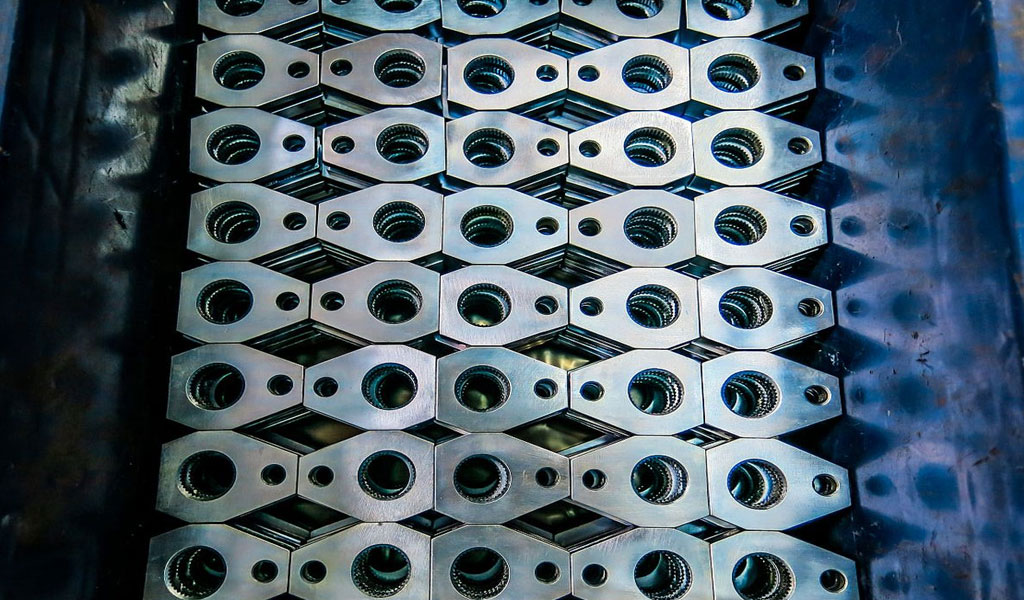
Firstly, etching processing is a non-mechanical contact method, preventing physical damage to the material’s surface and eliminating issues such as scratches and marks that may arise during traditional machining processes. This characteristic bestows etching technology with a unique advantage when dealing with precision and fragile materials.
Secondly, etching technology exhibits significant flexibility. It is not constrained by material hardness, allowing it to process a variety of materials regardless of their hardness. Furthermore, etching is suitable for various shapes of workpieces, whether flat, curved, or complex three-dimensional structures, enabling fine processing through etching techniques.
Additionally, etching technology is characterized by its diversity and cost-effectiveness. By adjusting parameters such as the type and concentration of the etchant, different etching effects can be achieved to meet diverse application requirements. Moreover, the relative simplicity of etching equipment and processes reduces manufacturing costs, enhancing the competitiveness of etching technology in the microelectronics industry.
Finally, etching technology boasts excellent controllability. By precisely managing the parameters of the etching process, accurate control over etching speed and depth can be achieved, ensuring quality and precision in the processing. This controllability enables etching technology to provide high precision and reliability in microelectronics manufacturing.
In conclusion, etching technology presents a broad spectrum of applications and significant advantages within the microelectronics industry. With ongoing advancements in science and technology and a growing demand for applications, etching technology is poised to play an even more crucial role in the microelectronics field, driving the continued development of the microelectronics industry.
Components That Are Produced By Etching Electronic Parts
The popularity of electronic makes it a desirable metal for use in fabrication because it is easy to manufacture and has favorable properties for many industrial products.With the photo etching process, the metal is etched evenly without any structural deformations from the hard tooling used in stamping and punching.Since there isn’t a heat point of contact like laser cutting, the parts’ metal properties remain unchanged and free from thermal deformations.Get inspired by our custom etching part projects and contact us to Get Instant Quote for rapid prototype or electronic etching parts start from 1pcs.
-
Aluminum Alloy 7075 Etched Microphone Grille
-
Etching 6.0 Inch Molybdenum Alloy Subwoofer Speaker Grill Guard Protector Cover for Home Audio
-
Aluminum Etching Car Audio Speaker Mesh
-
High Speed 316L Hair Dryer Mesh Etching
-
Etched Aluminum 7075 Bluetooth Headset Diaphragm
-
IC Lead Frame and VFD Dedicated Grid Etching
-
Metal Chemical Etching Reciprocating Razor Blades
-
Etching Bipolar Plates for Hydrogen Fuel Production
-
Stainless Steel 316 Metal Etched Paring Planer
-
Microporous Etching Stainless Steel 17-4 ph Speaker Mesh
-
Metal Etching Stainless Steel 430 Hair Dryer Air Outlet Net
-
Precision Etching 0.15mm Copper Laptop Vapor Chamber
-
Etched Beryllium Copper 17200 Lead Frames
-
Alumina Multi-Layered Board By Etching
-
0.078MM Nickel Solder Alloy Precision Resistor Sheet
-
0.3MM Laser Etched Titanium Mesh
Metal Etching Certification,Equipment List and Quality
We are committed to enlisting the full support of all employees to continuously improve our processes and enhance quality, thereby fulfilling our customer's needs with defect free products and services, on time and every time
- ISO 9001:2015 certified
- Compliance in DFARS materials sourcing requirements
- Strict compliance with PPAP and Process FMEA
- Fully compliant with the exacting requirements of our customers
- ITAR registered
- NIST cybersecurity standard compliant
- Proprietary Patented quality systems
- Skilled in KanBan and other customer driven quality and inventory management systems
Metal Etching Material
BE-CU is experienced in precision etching various metals, allowing customers the freedom to specify components in hundreds of different materials.
The Surface Treatment Of Metal Etching Parts
Do you want your etching parts to be more corrosion-resistant or get a specific look? Metal finishing service is a essential choice to achieve your design perfectly. BE-CU – metal-etch.com is an accomplished finished parts manufacturer, our workers and craftsman are capable to provide precision metal etching services and a wide range of finishing services including aluminum anodizing, painting, passivation, electroplating, powder coating, polishing, black oxide, conversion coating, abrasive blasting, etc. We offers several common surface finishes to help improve functionality and aesthetics.
- Anodizing (Anodized)
- Passivation
- Plating (Electroplating)
- Painting
- Black Oxide (Hot Blackening)
- Polishing
- Powder Coating
- Heat Treatment
- Satin Finish
- Abrasive blasting (Sandblasting)
- Conversion coating
- Tungsten carbide coating
After browsing a list of metal finishing services, select a process based on essential considerations, like production time, cost-effectiveness, part tolerance, durability and applications. High-tolerance metal etching parts are not recommended to apply secondary metal surface finish, because the treatment may change the sizes of the finished part through removing or adding a small amount of materials.
Other requirements or custom designs, welcome to contact us for a free quote fast!