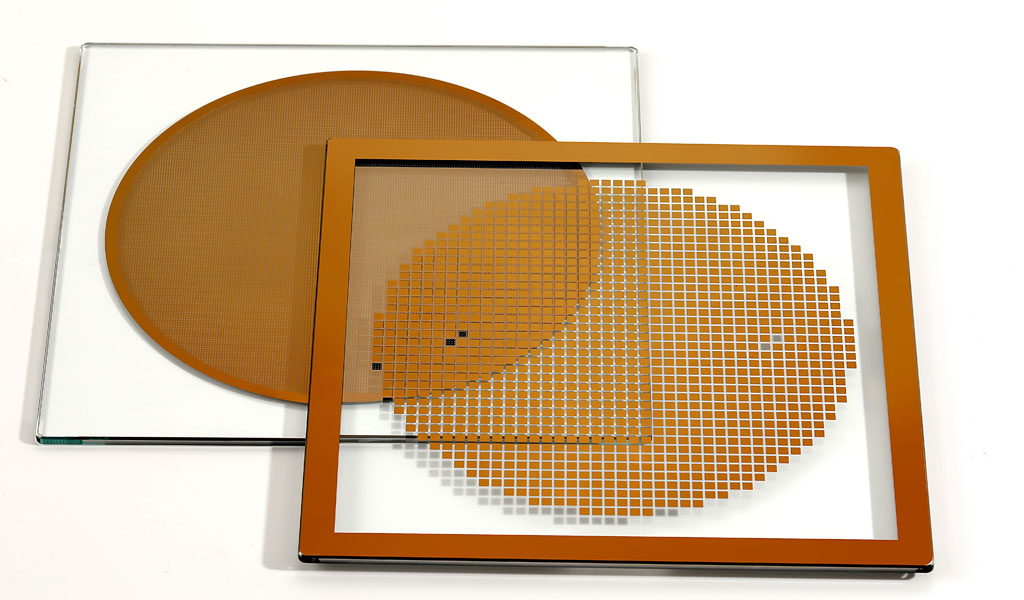
Photo-etched stainless steel code disks are precision components used in various industries, including aerospace, automotive, and electronics. These disks are manufactured through a process called photo-etching, which involves the use of photolithography to create intricate patterns on stainless steel sheets. The process is preferred for its ability to produce highly detailed and accurate parts with minimal material waste. However, the production of photo-etched stainless steel code disks is not without its challenges. This article delves into the common problems encountered during the production process and offers scientifically grounded solutions to mitigate these issues.
Common Problems in the Production of Photo-Etched Stainless Steel Code Disks
1. Surface Defects
Surface defects are a significant issue in the production of photo-etched stainless steel code disks. These defects can include scratches, pits, and uneven etching, which can compromise the functionality and aesthetic quality of the disks. The primary causes of surface defects are:
- Contamination: Dust, dirt, and other contaminants can adhere to the stainless steel surface, leading to uneven etching.
- Inconsistent Etching: Variations in etchant concentration, temperature, and exposure time can result in non-uniform etching.
- Mechanical Damage: Handling and transportation of the stainless steel sheets can introduce scratches and dents.
2. Dimensional Inaccuracies
Dimensional inaccuracies can occur due to several factors, including:
- Photoresist Issues: Inconsistencies in the application and development of the photoresist can lead to dimensional variations.
- Etchant Variability: Fluctuations in the etchant’s composition and temperature can affect the etching rate and uniformity.
- Thermal Expansion: Changes in temperature during the etching process can cause the stainless steel to expand or contract, leading to dimensional errors.
3. Chemical Residues
Chemical residues left on the surface of the stainless steel can affect the performance and longevity of the code disks. These residues can originate from:
- Incomplete Rinsing: Insufficient rinsing after the etching process can leave etchant residues on the surface.
- Photoresist Remnants: Inadequate removal of the photoresist can result in residual material on the disk surface.
- Contamination from Handling: Oils, greases, and other contaminants from handling equipment can transfer to the stainless steel surface.
4. Corrosion
Corrosion is a critical concern in the production of stainless steel code disks. Factors contributing to corrosion include:
- Environmental Conditions: Exposure to humid or corrosive environments can accelerate corrosion.
- Chemical Attack: Residual etchants and other chemicals can react with the stainless steel, leading to corrosion.
- Mechanical Stress: Stress corrosion cracking can occur due to mechanical stresses introduced during handling and processing.
Solutions to Production Problems
1. Addressing Surface Defects
To mitigate surface defects, the following solutions can be implemented:
- Cleanroom Environment: Utilizing a cleanroom environment can significantly reduce the risk of contamination. Cleanrooms are designed to maintain extremely low levels of particulates, such as dust, airborne microbes, aerosol particles, and chemical vapors.
- Consistent Etching Parameters: Maintaining consistent etching parameters, including etchant concentration, temperature, and exposure time, can ensure uniform etching. Automated etching systems can help achieve this consistency.
- Careful Handling: Implementing strict handling protocols, such as using gloves and clean tools, can minimize mechanical damage. Automated handling systems can further reduce the risk of scratches and dents.
2. Ensuring Dimensional Accuracy
To ensure dimensional accuracy, the following measures can be taken:
- Precise Photoresist Application: Using advanced coating techniques, such as spin coating or spray coating, can ensure a uniform layer of photoresist. Precise control over the photoresist thickness is crucial for achieving accurate dimensions.
- Temperature Control: Maintaining a constant temperature during the etching process can prevent thermal expansion and contraction, ensuring dimensional stability.
- Regular Calibration: Regular calibration of etching equipment can help maintain consistent etching rates and dimensional accuracy.
3. Eliminating Chemical Residues
To eliminate chemical residues, the following steps can be taken:
- Thorough Rinsing: Implementing a multi-stage rinsing process with deionized water can effectively remove etchant residues. Ultrasonic rinsing can further enhance the cleaning process.
- Complete Photoresist Removal: Using specialized stripping solutions and techniques, such as plasma ashing, can ensure complete removal of the photoresist.
- Contamination Control: Implementing strict contamination control measures, such as using clean gloves and tools, can prevent the transfer of oils and greases to the stainless steel surface.
4. Preventing Corrosion
To prevent corrosion, the following strategies can be employed:
- Controlled Environment: Maintaining a controlled environment with low humidity and minimal exposure to corrosive chemicals can reduce the risk of corrosion.
- Passivation: Applying a passivation layer to the stainless steel surface can enhance its corrosion resistance. Passivation involves treating the surface with a strong oxidizing agent to form a protective oxide layer.
- Stress Relief: Implementing stress relief techniques, such as annealing, can reduce mechanical stresses and prevent stress corrosion cracking.
Comparative Analysis of Solutions
The following table provides a comparative analysis of the solutions discussed, highlighting their effectiveness, cost, and implementation complexity.
Solution | Effectiveness | Cost | Implementation Complexity |
---|---|---|---|
Cleanroom Environment | High | High | High |
Consistent Etching Parameters | High | Moderate | Moderate |
Careful Handling | Moderate | Low | Low |
Precise Photoresist Application | High | Moderate | Moderate |
Temperature Control | High | Moderate | Moderate |
Regular Calibration | High | Low | Low |
Thorough Rinsing | High | Low | Low |
Complete Photoresist Removal | High | Moderate | Moderate |
Contamination Control | Moderate | Low | Low |
Controlled Environment | High | Moderate | Moderate |
Passivation | High | Moderate | Moderate |
Stress Relief | High | Moderate | Moderate |
Conclusion
The production of photo-etched stainless steel code disks is a complex process that involves numerous challenges. Surface defects, dimensional inaccuracies, chemical residues, and corrosion are among the most common problems encountered. However, by implementing scientifically grounded solutions, such as maintaining a cleanroom environment, ensuring consistent etching parameters, and applying passivation layers, these issues can be effectively mitigated. The comparative analysis provided highlights the effectiveness, cost, and implementation complexity of various solutions, offering a comprehensive guide for manufacturers to enhance the quality and reliability of their photo-etched stainless steel code disks.