Homepage » Metal Etching »
Beryllium Copper Etching – Etch Beryllium Copper Alloy
Beryllium copper, renowned for its unique combination of strength, conductivity, and corrosion resistance, has long been a material of choice in various industries, from aerospace and electronics to automotive and telecommunications. One of the most intriguing processes associated with this versatile alloy is etching, a method used to selectively remove material from the surface to create intricate designs, patterns, or functional components.
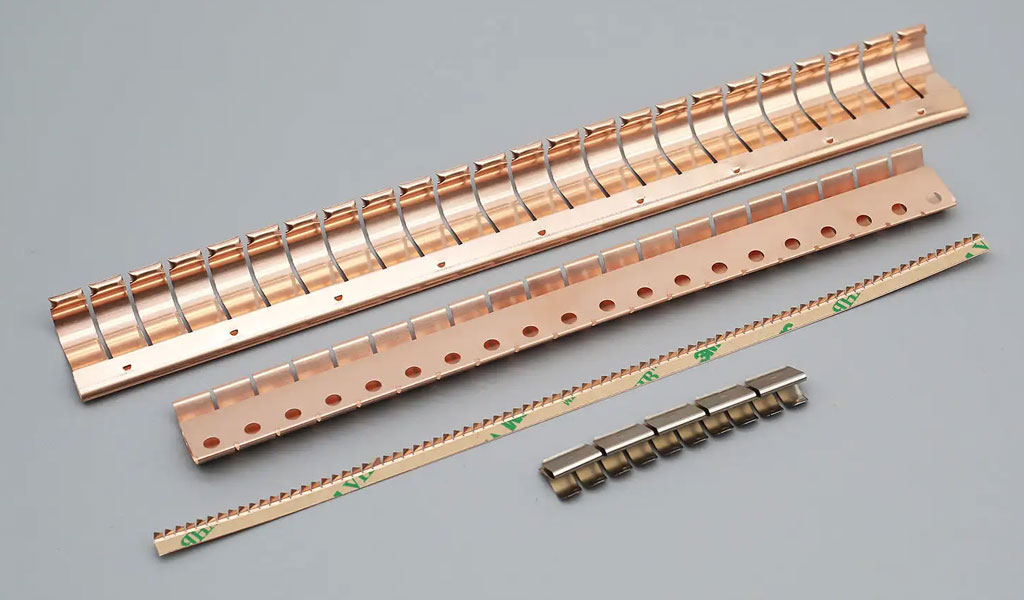
This alloy typically consists of copper as the base metal, with a small percentage of beryllium (usually around 0.5% to 3%) added to enhance its mechanical properties. The addition of beryllium improves strength, hardness, and thermal conductivity while maintaining excellent electrical conductivity and resistance to corrosion.Beryllium copper finds applications in various demanding environments where conventional materials may fall short. Its high strength-to-weight ratio makes it ideal for aerospace components, precision instruments, and electrical connectors requiring durability and reliability.Additionally, its resistance to fatigue and wear make it suitable for applications subjected to repeated stress or abrasive conditions.
Our Beryllium Copper Alloys Etching Service
At BE-CU ETCHING, we are equipped to create your Beryllium Copper Etching part from start to finish, including top-quality prototype and mass production.
In addition to performing high volume production, BE-CU Etching & Metal company can design, engineer, build prototypes, and test beryllium copper etched products to meet your unique specifications within a wide variety of industries.Our fabrication shop is uniquely designed to move raw materials in and finished goods out.Our ability to maintain total control of your project delivers increased quality and decreased turnaround times.We take pride in our ability to offer:
- Precision Etching Beryllium Copper C17200 (Alloy 25):
- Precision Etching Beryllium Copper C17510 (Alloy 3):
- Precision Etching Beryllium Copper C17500 (Alloy 10):
- Precision Etching More Beryllium Copper Alloys
With 30 decades in manufacturing, we have regularly served industries including aerospace, automotive, mass transportation, defense and solar. The versatility of our team, experience and equipment enables us to create just about any Beryllium Copper product you can conceive.
Components That Are Produced By Etching Beryllium Copper
The popularity of stainless steel makes it a desirable metal for use in fabrication because it is easy to manufacture and has favorable properties for many industrial products.With the photo etching process, the metal is etched evenly without any structural deformations from the hard tooling used in stamping and punching.Since there isn’t a heat point of contact like laser cutting, the parts’ metal properties remain unchanged and free from thermal deformations.Get inspired by our custom etching part projects and contact us to Get Instant Quote for rapid prototype or stainless steel etching parts start from 1pcs.
-
Copperplate Engravings Of World Famous Works
-
Artistic Etched Copper Shielding Electronics Playing Cards with Patterns
-
IC Lead Frame and VFD Dedicated Grid Etching
-
Ceramic Copper Clad Laminate By Precision Etching
-
Precision Etching 0.15mm Copper Laptop Vapor Chamber
-
Etched Beryllium Copper 17200 Lead Frames
-
Precision Etched Copper Alloy Leadframe
-
Beryllium Copper Etched Vibration Spring Leaf
Techniques for Beryllium Copper Etching
Beryllium copper’s unique properties present both opportunities and challenges in the etching process. Unlike pure copper, which readily reacts with common etchants such as ferric chloride or ammonium persulfate, beryllium copper is more resistant to chemical attack, requiring more aggressive etchants or specialized processes. Additionally, the presence of beryllium introduces health and safety considerations that must be addressed in handling and disposal of etchants and waste.
Several techniques are commonly employed for etching beryllium copper, each with its advantages and limitations:
Chemical Etching for Beryllium Copper
Chemical etching involves immersing the masked substrate in a corrosive solution that selectively dissolves the exposed areas of beryllium copper. Acid-based etchants, such as nitric acid or sulfuric acid mixtures, are commonly used due to their effectiveness in removing copper and beryllium oxides. However, these etchants can be hazardous to handle and require proper safety precautions and waste management procedures.
Electrochemical Etching for Beryllium Copper
Electrochemical etching, also known as electroetching or anodic etching, utilizes an electric current to accelerate the etching process. The substrate serves as the anode, while a cathodic electrode (e.g., stainless steel) is used to complete the circuit. Electrochemical etching offers precise control over the etch rate and allows for selective etching of complex shapes and features. However, it requires specialized equipment and may generate hydrogen gas, which poses safety risks in enclosed environments.
Laser Etching for Beryllium Copper
Laser etching employs a focused laser beam to selectively heat and vaporize the beryllium copper surface, resulting in material removal. This non-contact process offers high precision and repeatability, making it ideal for intricate designs and fine features. Laser etching is particularly well-suited for prototyping and low-volume production but may be less cost-effective for high-volume applications.
Applications of Beryllium Copper Etching
Beryllium copper etching finds diverse applications across various industries, leveraging the alloy’s unique combination of properties to meet specific performance requirements. Some common applications include:
Beryllium Copper Etching For Microelectronics
Beryllium copper’s excellent electrical conductivity and spring properties make it ideal for electrical contacts, connectors, and terminals in microelectronics devices such as smartphones, computers, and medical devices. Etching allows for precise patterning of contact surfaces and fine-tuning of electrical properties.
Beryllium Copper Etching For Precision Instrumentation
In precision instrumentation and metrology applications, beryllium copper etching is used to fabricate components such as strain gauges, flexures, and sensor elements with high dimensional accuracy and stability. The ability to etch complex geometries enables the customization of components to meet specific performance requirements.
Beryllium Copper Etching For Aerospace and Defense
Beryllium copper’s combination of strength, fatigue resistance, and corrosion resistance makes it well-suited for aerospace and defense applications, including aircraft components, missile guidance systems, and satellite communications. Etching allows for the fabrication of lightweight, high-strength structures and heat exchangers with intricate cooling channels.
Metal Etching Certification,Equipment List and Quality
We are committed to enlisting the full support of all employees to continuously improve our processes and enhance quality, thereby fulfilling our customer's needs with defect free products and services, on time and every time
- ISO 9001:2015 certified
- Compliance in DFARS materials sourcing requirements
- Strict compliance with PPAP and Process FMEA
- Fully compliant with the exacting requirements of our customers
- ITAR registered
- NIST cybersecurity standard compliant
- Proprietary Patented quality systems
- Skilled in KanBan and other customer driven quality and inventory management systems
Metal Etching Material
BE-CU is experienced in precision etching various metals, allowing customers the freedom to specify components in hundreds of different materials.
The Surface Treatment Of Metal Etching Parts
Do you want your etching parts to be more corrosion-resistant or get a specific look? Metal finishing service is a essential choice to achieve your design perfectly. BE-CU – metal-etch.com is an accomplished finished parts manufacturer, our workers and craftsman are capable to provide precision metal etching services and a wide range of finishing services including aluminum anodizing, painting, passivation, electroplating, powder coating, polishing, black oxide, conversion coating, abrasive blasting, etc. We offers several common surface finishes to help improve functionality and aesthetics.
- Anodizing (Anodized)
- Passivation
- Plating (Electroplating)
- Painting
- Black Oxide (Hot Blackening)
- Polishing
- Powder Coating
- Heat Treatment
- Satin Finish
- Abrasive blasting (Sandblasting)
- Conversion coating
- Tungsten carbide coating
After browsing a list of metal finishing services, select a process based on essential considerations, like production time, cost-effectiveness, part tolerance, durability and applications. High-tolerance metal etching parts are not recommended to apply secondary metal surface finish, because the treatment may change the sizes of the finished part through removing or adding a small amount of materials.
Other requirements or custom designs, welcome to contact us for a free quote fast!